WKU News
A Closer Look at Electro-Etching
- Sarah Redding
- Tuesday, April 24th, 2018
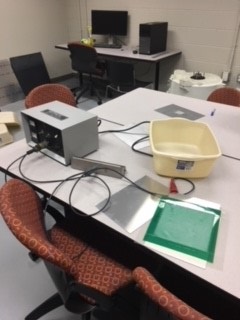
Four senior mechanical engineering students have been working to optimize electro-etching under the counsel of Dr. Morteza Nurcheshmeh for their senior project. I met with one of these students, Kristian Bogdanovic, to discuss the project’s stages and goals.
Bogdanovic began by explaining electro etching and its importance in testing the quality of raw materials when used with a video extensometer. A video extensometer measures the strength and quality of material by measuring changes in the material as it is stretched to breaking. Usually this includes marking the material with dots that are warped as the material is stressed, and the amount of warping helps determine the material’s quality. Therefore, it is important that markings are clear and dark enough to ensure they are detected by the extensometer, and markings can be made in a variety of ways, including with an electro-etching machine.
Bogdanovic reported that this senior project was developed because Dr. Nurcheshmeh used the university’s electro-etching machine for a project, but found that it didn’t produce clear results. Therefore, Dr. Nurcheshmeh tasked the four participating students with researching possible alternative marking methods and optimizing the settings on the electro-etching to increase efficacy and clarity of etches.
According to Bogdanovic, the team’s work on the project has been completed in two primary stages. Last semester was devoted primarily to researching and testing possible alternatives. The team explored laser etching, physical cutting, screen printing, and chemical etching. The team considered cost, accessibility, and efficacy. Laster etching was determined to be too expensive because clear cuts require a very powerful laser. Physical cutting didn’t produce markings with the same clarity as electro-etching. Screen printing was determined to be inexpensive, but markings were prone to smudging. Chemical etching was also determined to be cost prohibitive and requires special safety considerations.
Therefore, the team chose to move forward with their project this semester by optimizing the settings of WKU’s existing electro-etching machine.
The electro-etching machine is a small box that sends an electrical current through a roller. This roller is passed along a wick (a spongy material that is soaked in an electrolyte, usually saltwater) that sits atop a stencil on a steel or aluminum plate. The electrical current passes through these layers, etching an image or pattern on the plates. Several factors influence the quality and clarity of the resulting image or pattern, including pressure, speed, electrolyte solution, and current settings.
Bogdanovic and his teammates have completed about 20 tests so far, and plan to have about 40 test samples for the final project.
Bogdanovic, who reported that a video extensometer is used at his current job, has enjoyed working with his teammates and the connection to his current work.
Some of the links on this page may require additional software to view.